0:00
/
Before you continue to YouTube
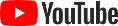
Hi guys, Hope you all had a great 'New Year'....trying out the 'slideshow' option...here's the first for the tender..hope to get back on the build during next week.....cheers...:)
Posted by Building a 5" gauge model of 4472 Flying scotsman on Saturday, 7 January 2017
tried another for loco with less photo's. last was too bad a quality....
Posted by Building a 5" gauge model of 4472 Flying scotsman on Saturday, 7 January 2017
0:00
/